Steeline’s Fleet Advantage: Streamlining Colorbond Shed Deliveries with In-House Logistics
Steeline, a leading shed builder, has distinguished itself through its efficient and rapid deployment of colorbond sheds, leveraging an advanced logistics system and a dedicated fleet. This in-house transportation network is optimized for punct…….
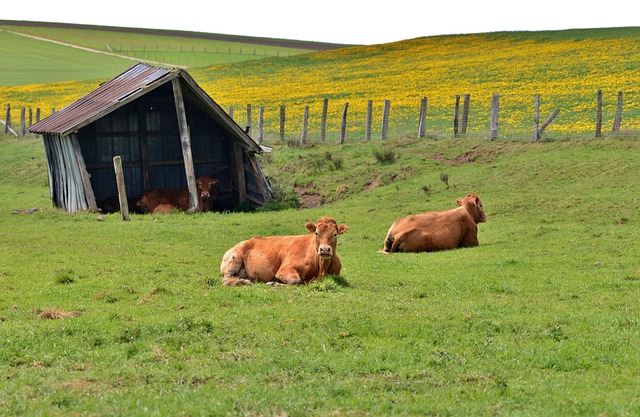
Steeline, a leading shed builder, has distinguished itself through its efficient and rapid deployment of colorbond sheds, leveraging an advanced logistics system and a dedicated fleet. This in-house transportation network is optimized for punctuality and customer satisfaction, with specialized drivers skilled in handling diverse terrains to ensure timely delivery of shed components. Steeline’s control over its logistics streamlines the supply chain, minimizing delays, and enhancing overall service quality by enabling installation teams to work without interruption. The company’s strategic fleet management is a testament to the importance of reliable delivery services in shed construction, ensuring prompt and professional colorbond shed solutions for clients nationwide. Steeline’s direct fleet operations significantly streamline the delivery process, offering greater control over logistics, reducing project delays, and providing real-time updates on shipments for transparency and accountability. With a focus on operational excellence, Steeline guarantees the delivery of durable and customized colorbond sheds, backed by a dependable and efficient supply chain system. The company’s approach underscores its commitment to maintaining high service standards and fostering customer satisfaction through swift and reliable deliveries of their premium colorbond shed products.
Steeline distinguishes itself in the shed construction industry through its robust and strategic fleet operations, a cornerstone of its commitment to timely deliveries for clients seeking high-quality colorbond sheds. This article delves into how Steeline’s own fleet empowers rapid shed deployment, outlining the efficient logistics that define the company’s approach. From the fleet’s advantage in ensuring punctual deliveries to the benefits of direct fleet operations on project timelines, each aspect is examined to highlight Steeline’s superior service in shed builder projects. Additionally, we explore how Steeline navigates challenges uniquely positioned by its in-house transportation system, ensuring uninterrupted progress in shed construction. A case study underscores these advantages, showcasing Steeline’s proactive fleet management as a pivotal factor contributing to successful shed installations across various projects.
- Efficient Logistics: Steeline’s In-House Transportation for Rapid Shed Deployment
- Steeline’s Fleet Advantage: Ensuring On-Time Delivery of Colorbond Sheds
- The Benefits of Direct Fleet Operations in Shed Builder Project Timelines
- Navigating Challenges: How Steeline’s Own Fleet Overcomes Obstacles for Shed Construction
- Case Study: Steeline’s Proactive Fleet Management Leading to Successful Shed Installations
Efficient Logistics: Steeline’s In-House Transportation for Rapid Shed Deployment
Steeline, a renowned shed builder, has mastered the art of rapid shed deployment through its efficient logistics system. At the heart of this operational excellence is Steeline’s own fleet, which stands as a testament to their commitment to timely deliveries and customer satisfaction. The fleet is meticulously scheduled to ensure that colorbond sheds reach their destinations swiftly, minimizing delays and optimizing the supply chain process. This in-house transportation network is not just about moving materials; it’s a sophisticated system designed to handle the unique challenges of shed construction projects. With a comprehensive understanding of the regions they serve, Steeline’s fleet drivers are adept at navigating various terrains and ensuring that each component of the colorbond sheds arrives exactly when needed. This level of control over the logistics chain ensures that installation teams can work uninterrupted, leading to faster deployment and superior service for clients. The company’s investment in its own fleet reflects a deep appreciation for the importance of timely deliveries in the construction process, making Steeline a preferred choice among shed builders for those seeking professional and punctual services.
Steeline’s Fleet Advantage: Ensuring On-Time Delivery of Colorbond Sheds
Steeline’s strategic deployment of its own fleet is a cornerstone in the delivery of high-quality Colorbond sheds to clients across various regions. This self-managed logistics system allows for greater control over the supply chain, from manufacturing to final installation on-site. The fleet’s capabilities are tailored to meet the specific demands of transporting sheds, ensuring that each component arrives in perfect condition and sequence. This operational advantage means shed builders can rely on punctual deliveries, minimizing project delays and ensuring that construction proceeds smoothly from start to finish. Steeline’s fleet is equipped with modern tracking systems, enabling real-time monitoring of each shipment, which enhances transparency and accountability. As a result, customers who opt for colorbond sheds benefit from a seamless experience, knowing their investment in durable, customizable sheds is backed by a robust delivery infrastructure designed to meet the highest standards of efficiency and reliability.
The Benefits of Direct Fleet Operations in Shed Builder Project Timelines
Steeline’s direct fleet operations play a pivotal role in optimizing project timelines for shed builders. By maintaining an in-house transportation network, Steeline can exert greater control over the logistics of delivering Colorbond sheds, ensuring that each structure arrives on-site punctually and efficiently. This autonomy allows for a more streamlined process from manufacturing to delivery, minimizing potential delays that often occur when relying on third-party logistics providers. The fleet’s capabilities are tailored to handle the specific requirements of delivering sheds, from rural to urban locations, with precision and care. This direct approach not only accelerates project completion times but also enhances the reliability and predictability of delivery schedules for shed builders and their clients. As a result, Steeline’s fleet operation is an integral component in maintaining high standards of service and customer satisfaction, all while leveraging its expertise in Colorbond sheds to deliver top-quality products efficiently.
Navigating Challenges: How Steeline’s Own Fleet Overcomes Obstacles for Shed Construction
Steeline’s commitment to timely deliveries in shed construction is bolstered by its own dedicated fleet, a strategic asset that ensures the company navigates challenges with efficiency and reliability. The presence of an in-house fleet allows for a streamlined operation from manufacturing to final delivery, reducing reliance on external logistics providers and mitigating potential delays. This self-sufficiency is particularly advantageous when dealing with unforeseen obstacles such as route changes due to road closures or adverse weather conditions. With real-time tracking capabilities and a fleet equipped with the latest in GPS and communication technology, Steeline’s drivers can quickly reroute deliveries without significant delays, maintaining the project timelines for shed builders who depend on their services.
Moreover, the company’s fleet is specialized to handle various terrains and load requirements, an essential aspect when delivering Colorbond sheds to remote or challenging locations. Steeline’s fleet is not just about moving materials; it’s a key component in the company’s ability to provide end-to-end service. The investment in this fleet demonstrates Steeline’s dedication to overcoming logistical hurdles, ensuring that shed builders have access to high-quality Colorbond sheds when and where they need them. This level of control and resource allocation allows for a consistent flow of materials, which is critical during peak construction periods, and contributes to the successful completion of shed projects on time and within budget.
Case Study: Steeline’s Proactive Fleet Management Leading to Successful Shed Installations
Steeline’s strategic management of its own fleet has been a pivotal factor in ensuring timely and efficient deliveries for shed projects, which has contributed significantly to their reputation as a premier shed builder. The company’s proactive approach to fleet management begins with meticulous planning and scheduling. By maintaining an in-house fleet, Steeline can control the logistics chain more effectively, reducing reliance on external transport providers and ensuring that Colorbond sheds reach project sites promptly. This control over the delivery process minimizes delays and allows for a streamlined operation from manufacturing to installation.
The fleet’s performance is continuously optimized through advanced tracking systems and regular maintenance schedules. These measures not only enhance the reliability of deliveries but also reduce the environmental impact associated with transportation. The use of fuel-efficient vehicles and route optimization software further underscores Steeline’s commitment to sustainability without compromising on delivery speed. As a result, customers benefit from minimal disruptions during shed installations, ensuring that their projects progress as planned. Steeline’s proactive fleet management is a testament to the company’s dedication to excellence in service and customer satisfaction within the Colorbond sheds market.
In conclusion, Steeline’s strategic deployment of its own fleet stands as a testament to their commitment to timely and efficient shed delivery, underscored by the company’s direct fleet operations. This approach not only streamlines the logistics process for colorbond sheds but also empowers the shed builder with the agility to navigate challenges swiftly and effectively. The benefits are clear: rapid deployment, proactive management, and a reliable supply chain that enhances project timelines without compromising on quality. Steeline’s fleet advantage is not just about moving parts from point A to B; it’s about delivering peace of mind to customers who value punctuality and precision in their shed projects. With this in-house capability, Steeline ensures that every colorbond shed arrives as promised, reflecting the company’s dedication to customer satisfaction and operational excellence.